Service Aids - More Than You Think!
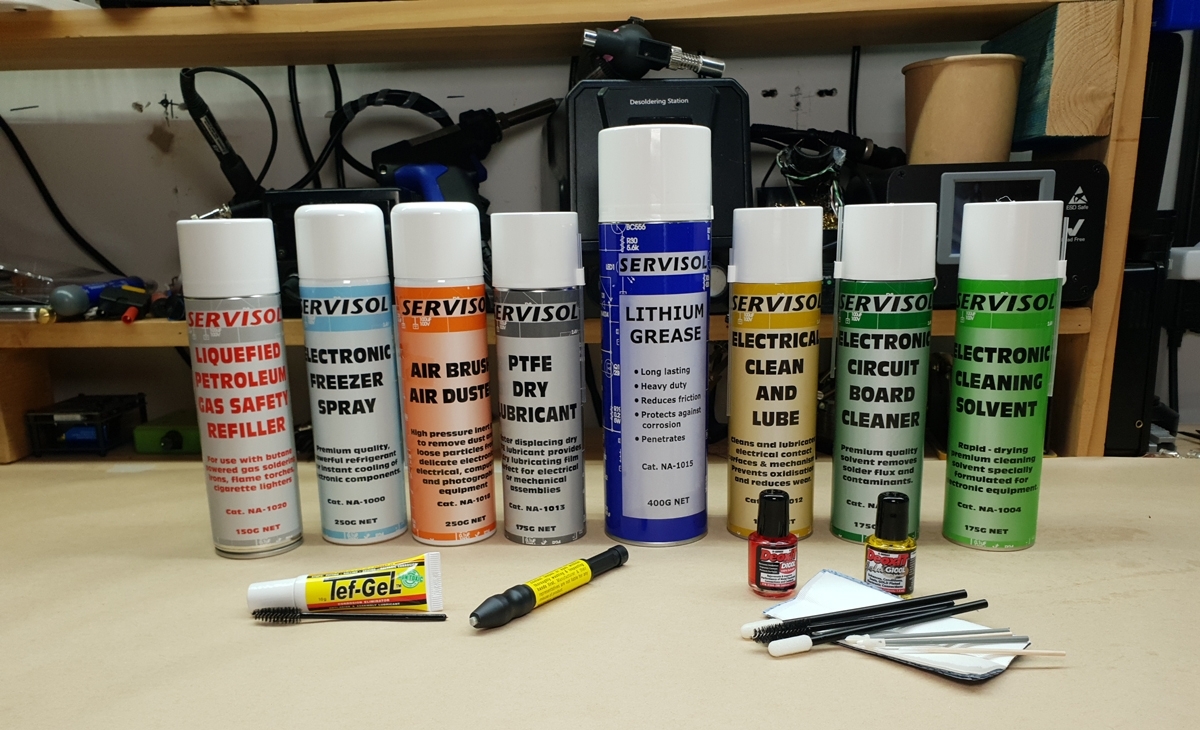
Summary
From WD40 to Superglue, grease to degreaser, service aids are an essential part of any toolbox or workshop. However, some are very misunderstood or just not well known. We are going to cover off some that sound the same but are different, some that many people don't know the use for (and the benefits of), and some that you may have been missing all your life!
Materials Required
1 | Electronic Cleaning Solvent Spray Can | NA1004 |
1 | Electronic Circuit Board Cleaner Spray Can | NA1008 |
1 | Contact Cleaner Lubricant Spray Can | NA1012 |
1 | Dust Remover Spray Can | NA1018 |
1 | Freezing Spray Can | NA1000 |
1 | Dry Lubricant Spray | NA1013 |
1 | Lithium Grease 400g | NA1015 |
1 | Butane Gas Can | NA1020 |
1 | Corrosion Buster Pen | NA1410 |
1 | Tef-Gel 10ml Tube | NA1040 |
1 | DeoxIT Contact Cleaner and Rejuvenator - Solution Kit | NS1436 |
Table of Contents
- Contact Cleaner Vs Cleaning Solvent Vs Circuit Board Cleaner
- Air Duster Cans - Not Air At All!
- Freeze Spray Can Save You Hours!
- Lesser Known Lubricants Could Change Your Life
- Dry Lubricant - Life Teflon, But Not Teflon
- Lithium Grease - Your New Universal Grease
- NA1020 Liquified Petroleum Gas Safety Refiller
- Clearning Corrosion With The Corrosion Buster Pen
- TEF Gel Corrosion Proventer
- Cleaning Contacts with the Deoxit Contact Cleaner Kit
Very different products with similar names.
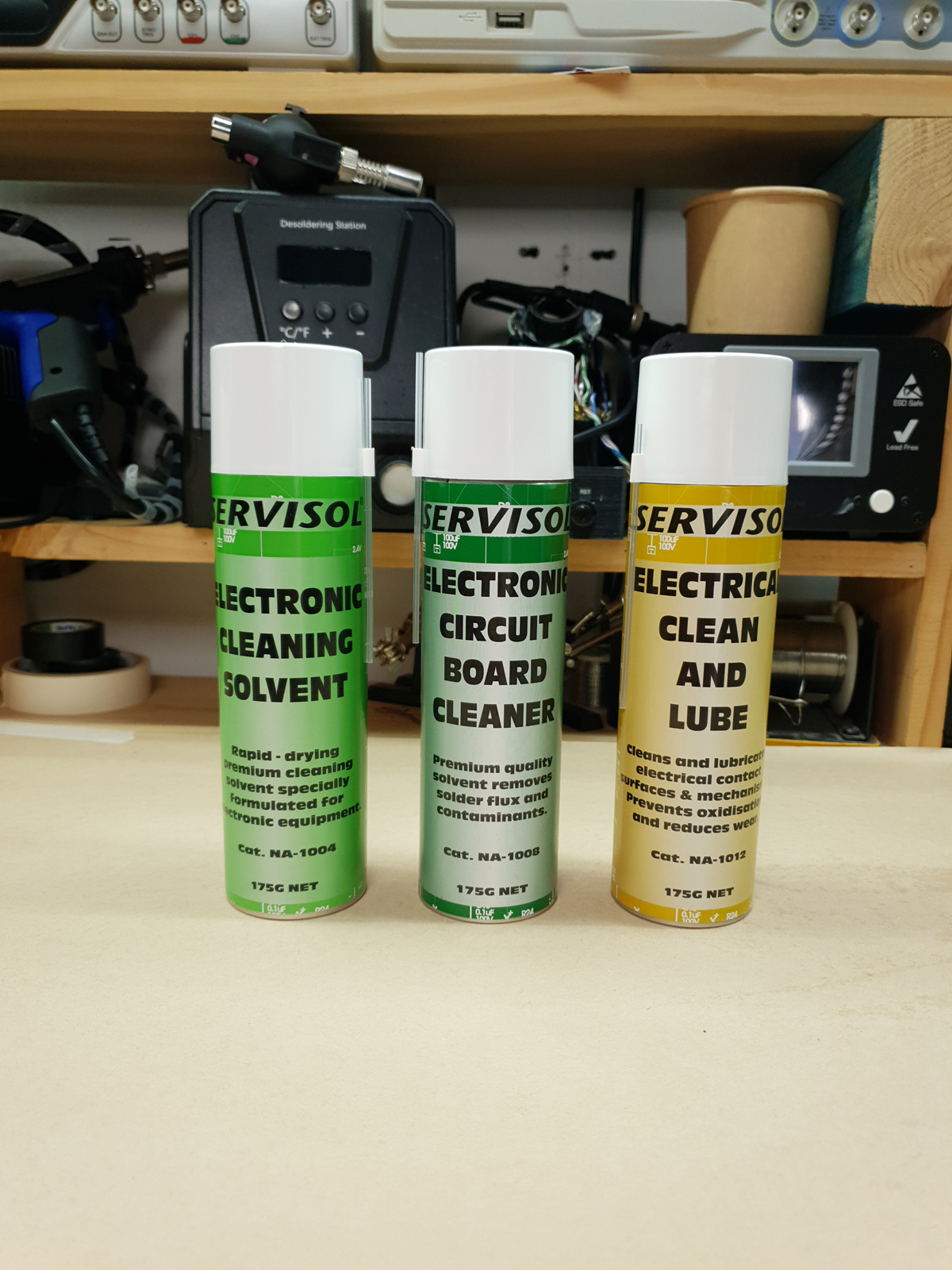
When it comes to maintenance cleaning, these three products are often confusing. Many people assume they are the same thing with a different label, but that could not be further from the truth! Each is a specific combination of cleaners and supporting products that do a similar job but in very different circumstances.
The most confusing pairing is 'Electronic Cleaning Solvent' next to 'Electronic Circuit Board Cleaner'.
'Electronic Cleaning Solvent' NA1004 is for general cleaning of electronic equipment, not circuit boards themselves. It contains the gentlest of the solvents in these three products, and is meant for cleaning the outer surfaces or things like heatsinks. It removes fingerprints, light oils, dust and moisture from things that get handled. It is not meant to be sprayed on circuit boards directly, but it will not damage them if it is. It is designed to leave minimal to no visible residue. Use it next time you want to remove the buildup from your keyboard, but remember to unplug or turn off the keyboard first!
'Electronic Circuit Board Cleaner' NA1008 is meant to be sprayed on a circuit board, rather than on equipment. It is aimed at dissolving and removing soldering flux, including the residue from rosin/resin-cored solder, as well as other construction contaminants. It is safe for most plastics but not all, and unlike Electronic Cleaning Solvent above, it can leave a residue. It is not designed for aesthetic cleaning, but rather for removing problem contaminants and residues from operational electronics parts and boards. Note, that is 'operational', not 'operating'. Turn it off first! Use it to clean up a circuit board after soldering to avoid leakage in RF circuits due to resin and fingerprints, or to clean up a greasy or dirty old circuit board prior to fault-finding or repairs.
'Electrical Clean and Lube' is the last of the trio, and one of the most misunderstood. This is not designed for electronics at all, as the 'electrical' in the name may hint at. In fact, if you use it on a circuit board, it will cause you headaches and nightmares. This product is a heavier-duty cleaner that also has lubrication built in. It is designed for cleaning and improving contacts, like those inside switches or relays. The idea is that the cleaning solvents carry away grease and oil, dirt, corrosion, moisture and residues, and the lubricant coats the contacts to help them stay free of corrosion, moisture, and unwanted build-ups. It works really well on the things it is meant for: Switches, relays, and connectors, or anything else with a contact surface. The oil left behind does not interfere with conductivity, except on small or weak electronic signals. Do not use it on low power connectors like headphones or HDMI connectors! Do use it on switches, trailer connectors, cigarette lighter plugs, or anything of that nature. Do not use it on electronics! The oily lubricant left behind will attract dust to the circuit board (which is a very different surface and environment compared to a switch or plug) and eventually, the dust will build up moisture. The solvents are also not gentle, and can cause damage to sensitive electronics. That is one of the more common mistakes our staff see.
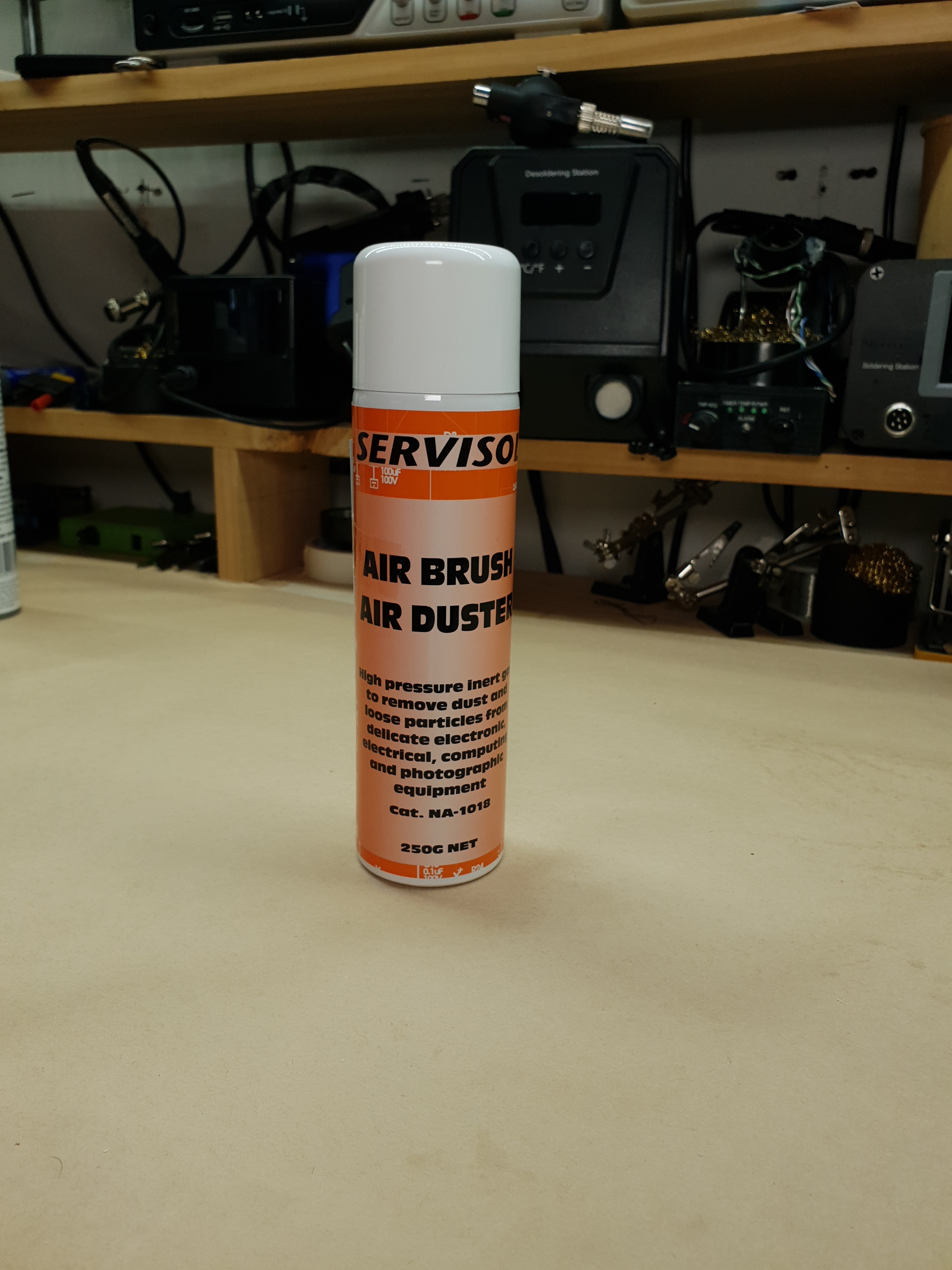
Many people misunderstand canned air products. Not so much what they are used for, but what they really are and why you would use them over cheaper products or just a compressor or blower. The NA1018 Air Duster is not air at all. It is a blend of inert gases designed to avoid some serious problems. Using compressed air for cleaning electronics has some problems. Firstly, it has a habit of introducing moisture. The physics lesson that explains this is beyond this article, but if you look at industrial compressor systems for, say, pneumatics in factories or the like, they have air dryers in the lines. These are absent on most home compressors and definitely on blowers.
The other major problem is static electricity. Air is not inert and carries a charge. Moving it fast can cause this charge to build up, both by the action of the molecules of the gases that make up the air like water droplets in a cloud do to make lightning, and by sheer volume of air moving past lesser-charged electronics. So, in short, using compressed air to clean a circuit board can cause static damage.
While some cheap air duster cans are just compressed air, and many are not even dried, NA1018 Air Duster is, in fact, not air at all. It is a carefully chosen blend of gases that are inert and not electrically charged; and they are also dry and do not absorb and transfer moisture. However, the propellant is a refrigerant gas and the active product (the inert blend) is semi-liquid in the can, so if you hold it upside down or too far to the side, liquid will come out. This is very cold, akin to freezing spray, so be warned!
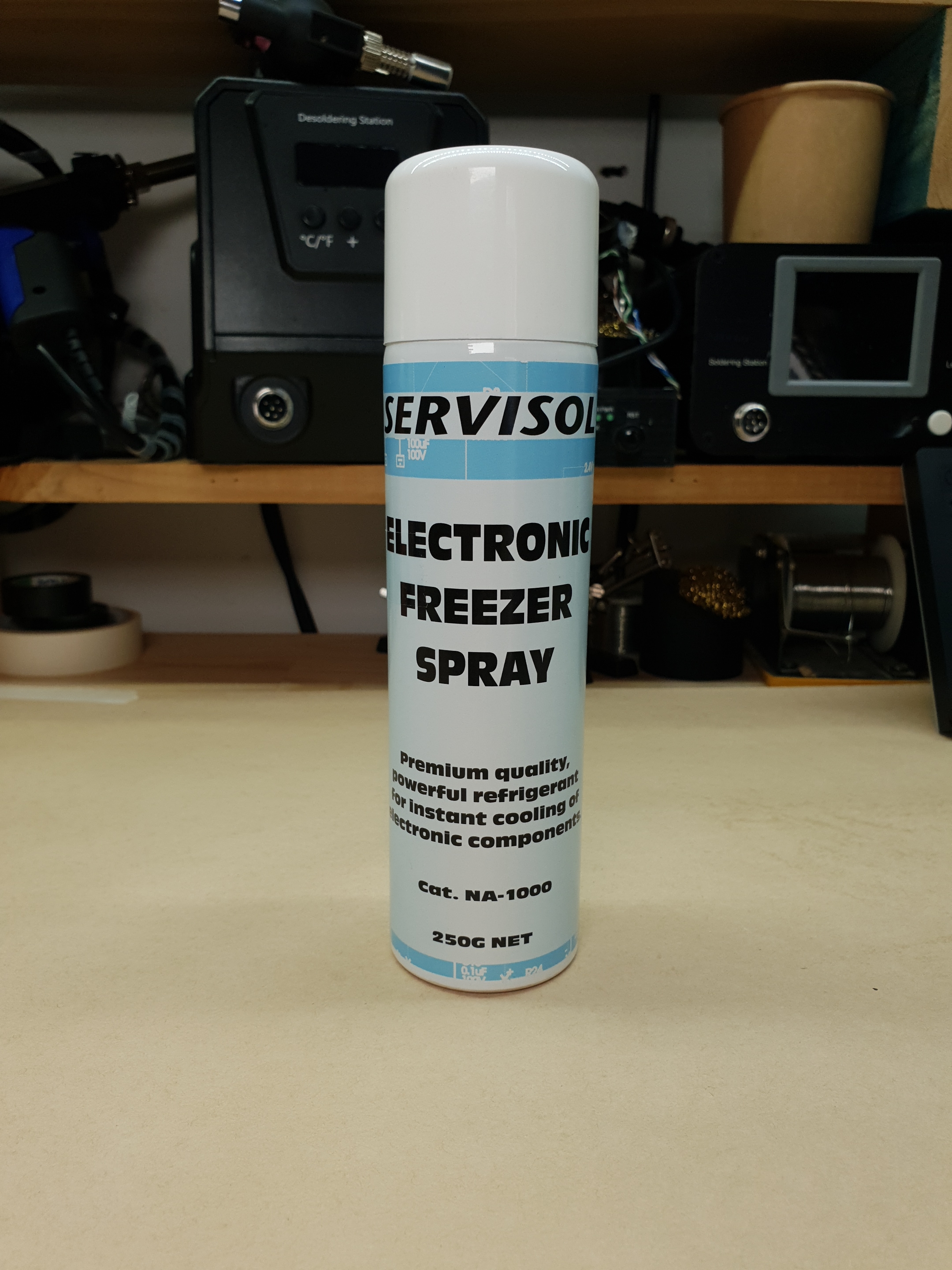
NA1000 Freezer spray is another one of those products that many people don't know the use for, and you could really be missing out! In short, it is for thermal fault-finding. Many problems with electronics (and indeed further afield) occur during change of temperature. Freezer spray is used in conjunction with a heat gun, hair dryer, or similar, to test for faults. Aim it at the circuit under test, in the place where you suspect a fault, and chill that area. If the fault appears (or disappears, as is sometimes the case), you have narrowed down the area or even isolated the problem. Heating the circuit with the hair drier or similar is the counter-step, as some faults present on warm-up or when equipment is overheated. This heating and cooling cycle suits an array of different intermittent faults, and some will be found while freezing, while others will be discovered when warming back up.
Other uses for freezing spray include causing parts to contract when trying to interference-fit (friction fit) tight parts (heat the outer part, freeze the inner part); and making old, degraded rubber or grease go hard when trying to scrape it off something.
When we talk about lubricants, many people think of WD40, motor oil, axle grease, and the kind of light oil you use to fix things around the house. However, in some circumstances, you will need something more specialised, but many people do not know that.
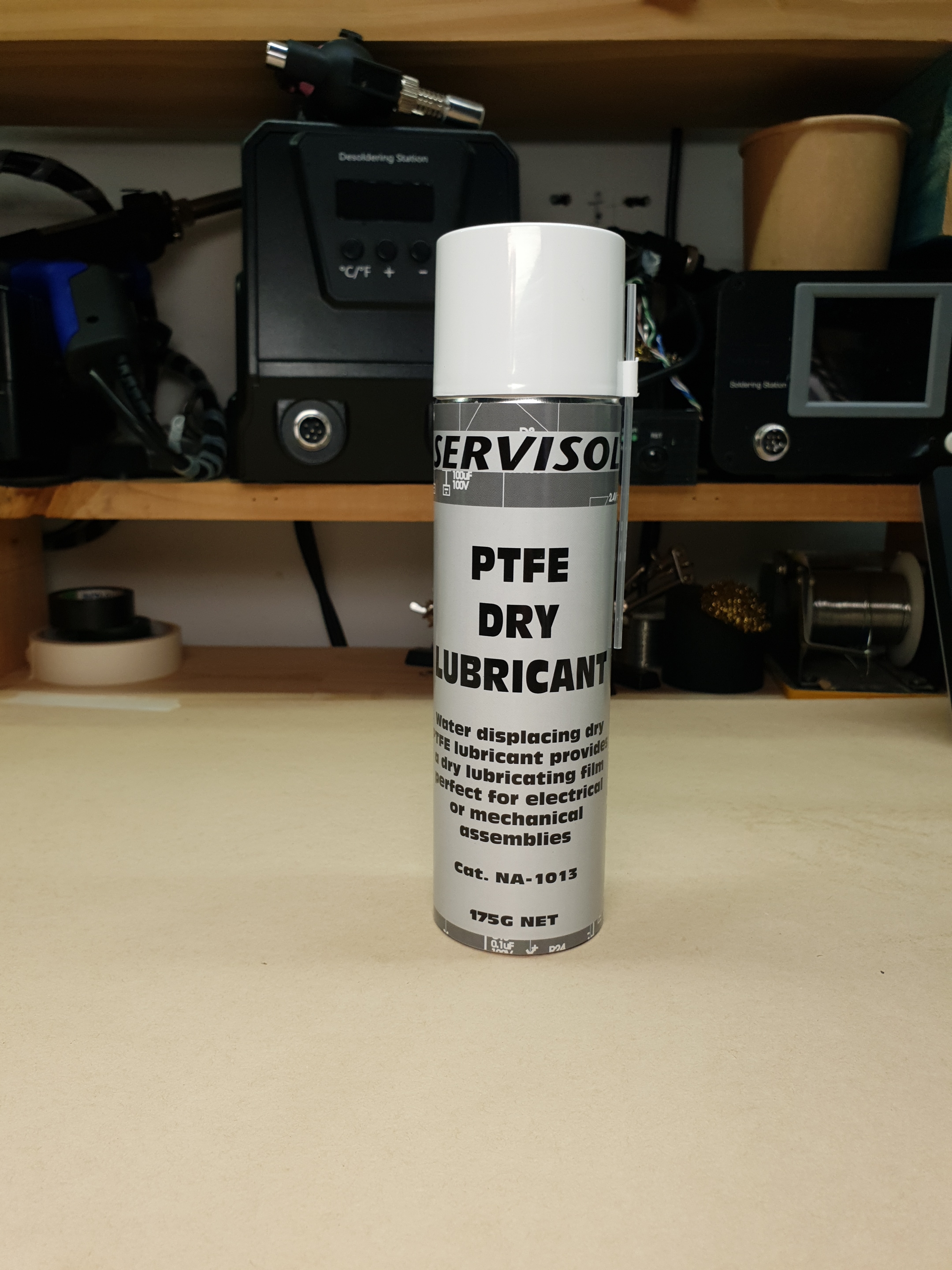
There are situations where having oil or grease on something causes dust or other mobile particulate contaminants to build up. A great example is when people use oils to lubricate door hinges or worse, locks! Dust builds up on the door hinges by sticking to the oil, and while on the hinge that looks unsightly, on the lock it causes jamming.
In other cases, the liquid oil does not stay where it should, like vertical situations such as office chair gas lifts. These also suffer from the dust build-up problem on top of that, which gets into the seals when you put the chair down. While some vertical situations can be fixed by using grease, which sticks and does not run, that is often a poor solution.
The answer is NA1013 PTFE dry lubricant. PTFE is Polytetrafluoroethylene, and it is a very complex polymer that is physically very similar to Teflon. Teflon was the famous non-stick product of the 80s, but one tiny detail in the chemical structure meant that it can cause cancer. PTFE is chemically similar enough to have the same physical non-stick properties, but different enough that it is currently not known to science to be a cause of cancer.
NA1013 Dry Lubricant is PTFE dissolved in solvents. It sprays on as an aerosol, then the solvents dry, leaving a film coating of PTFE that does not run down vertical surfaces, attract dust, or slowly dry up and go hard like many greases. It is great for any situation where you need things to slide smoothly, but where dust or run-off would be an issue. It can replace graphite powder in lock and hinge lubrication, too. However, it can leave a white residue so be careful about overspray in visible locations.
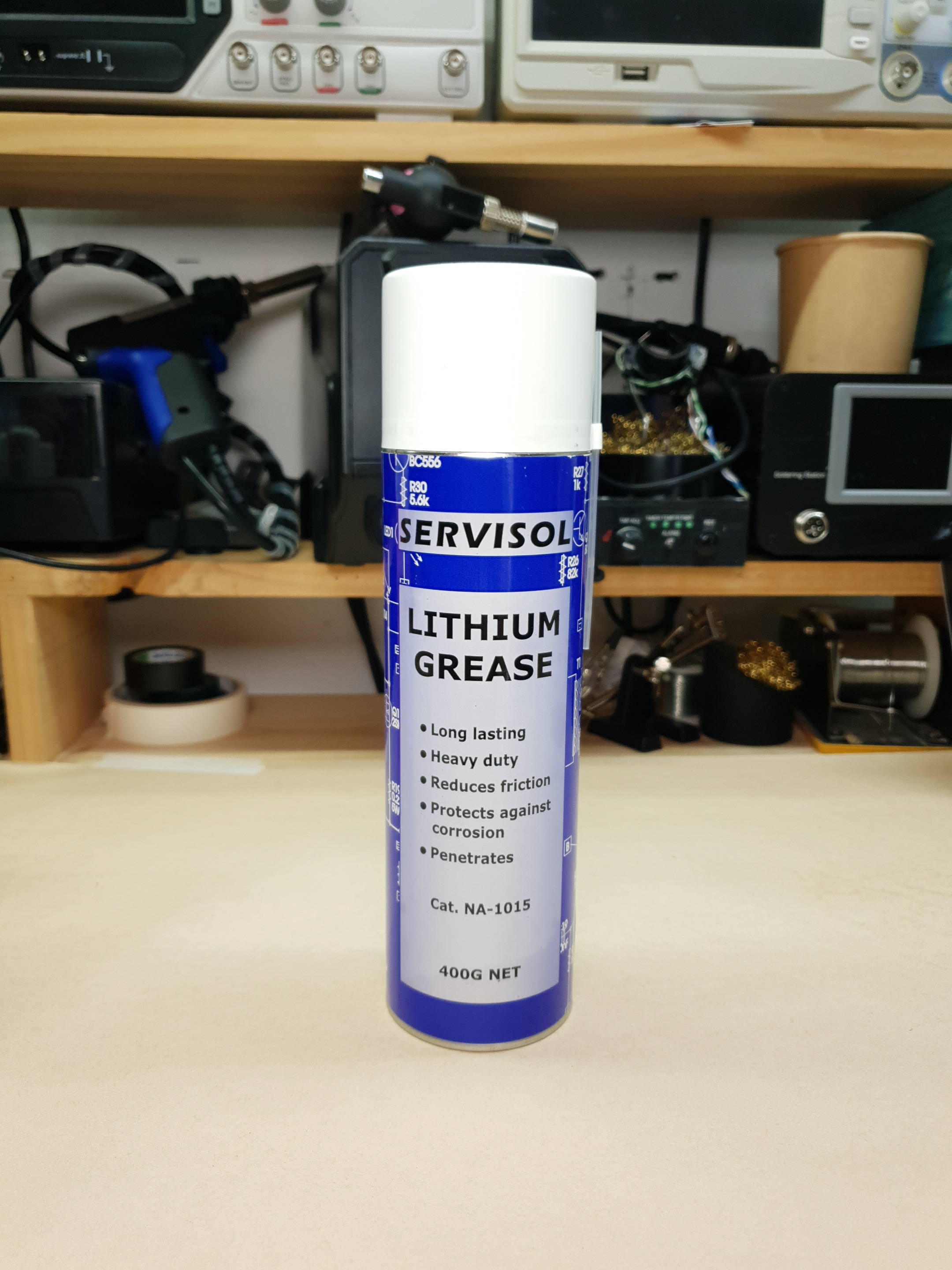
NA1015 Lithium Grease is a different beast altogether. It is actually the world's most common grease, accounting for over 75% of use, but much of this is industrial and many people still do not know about it. Grease is not just heavy oil. It is a base oil, a thickener, and performance additives. In Lithium grease, Lithium is the thickener, with normal petrochemical oils being the base. Do not worry, it won't catch fire like Lithium batteries.* However, Lithium grease has properties of several different types of grease, which is why it is referred to as a universal grease.
Compared to many other types of grease, Lithium grease has great adhesion. In fact, be careful with it, because cleanup can be painfully hard. This makes it great for elevated or moving parts. It is very water resistant, but also temperature resistant. In older styles of grease, often calcium greases were used for adhesion and water resistance, while sodium greases were for temperature resistance. In addition, it is great at corrosion resistance.
This makes Lithium grease perfect for applications where metal-on-metal bearing surfaces have a lot of heat, movement, or water exposure. As a particular example, we used it to lubricate the mechanical linkage of a split-shaft petrol outdoor power tool. The power head can be connected to a line trimmer, hedge trimmer, or pole chainsaw, all of which have lithium grease in the joints of the drive mechanism. This joint gets quite hot when working, and there is a lot of metal-on-metal pressure.
* As an aside to the introduction, it is actually the Cobalt compounds in Lithium Ion batteries that cause fires, which is why Lithium Iron (or Ferro) Phosphate batteries do not carry the same fire risk.
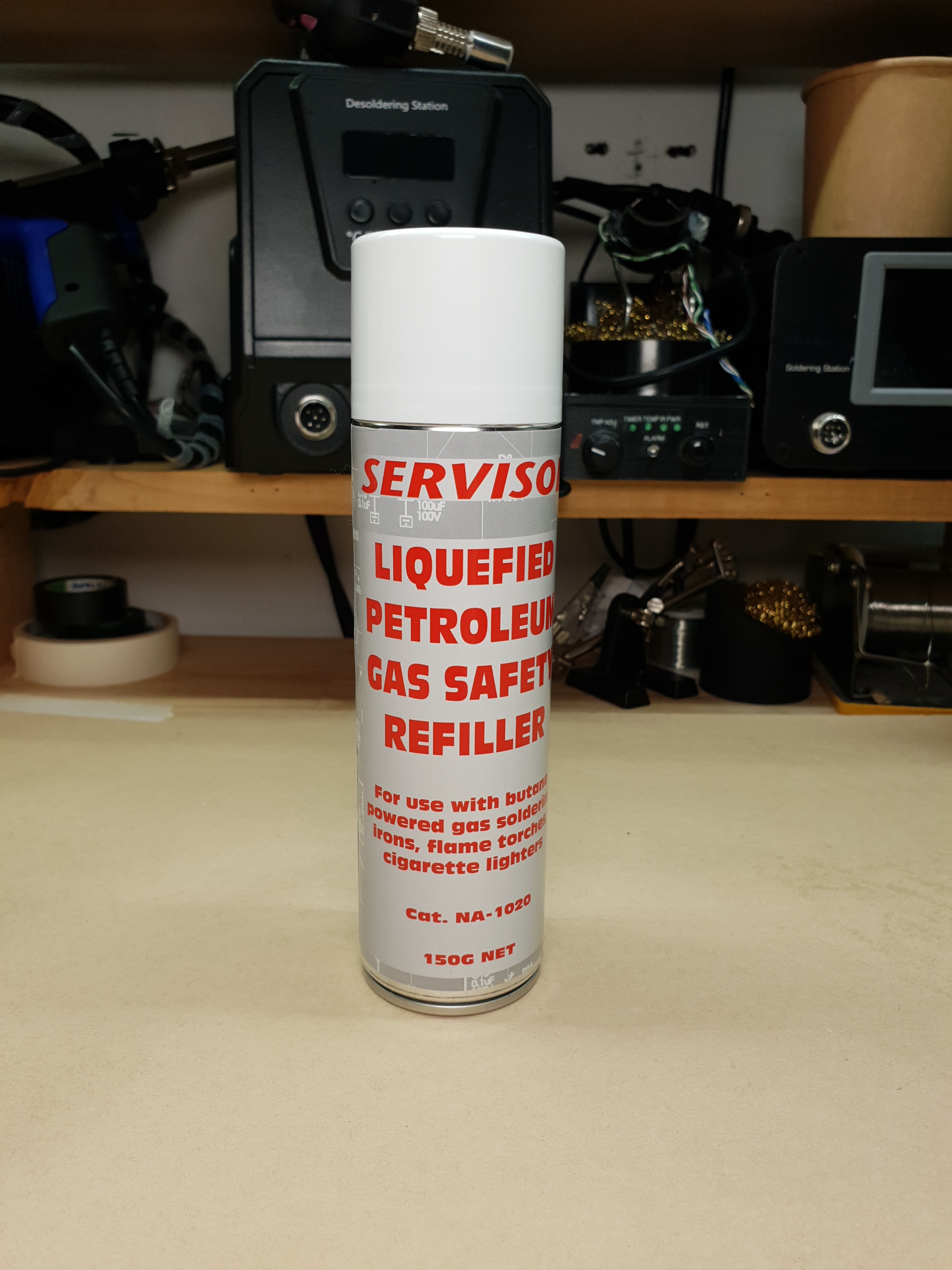
The use of this one is pretty obvious, but every few weeks our store team get asked by someone why they can't get their lighter or soldering iron to fill. The problem is technique. The can is just full of low-pressure liquified gas. By the way, 'low pressure' is a relative term when it comes to liquified gas. The butane, propane, and pentane that typically makes up these refills are fairly heavy in gas terms and so need less compression to stay liquid. However, they will expand with reasonable pressure. For that reason, the product is also its own propellant!
There is no tube inside the can like a normal aerosol, and this accounts for most of the misunderstandings about use. Many people try to fill the can by holding it under the tool or lighter. In fact, the lighter or tool must be held downwards and the can used upside down! Then, the liquid will be pushed out of the nozzle and into whatever you are trying to refill.
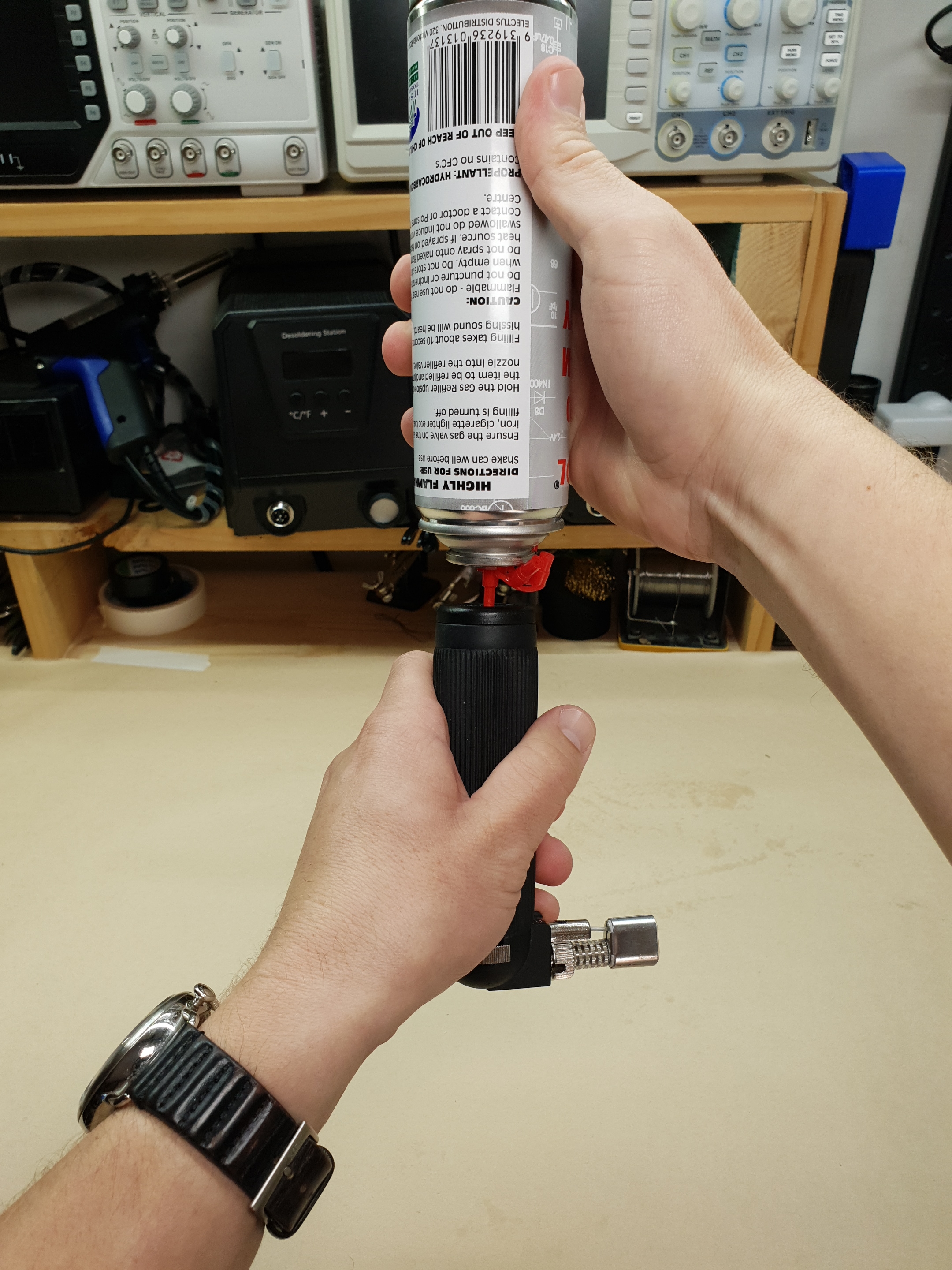
In addition, it is critical to fit the right adaptor. The can comes with a ring of adaptors to suit different fill valves. Most fill halves have a sprint closure that needs to be depressed mechanically by pushing the adaptor or can nozzle into it. In some cases, an adaptor will fit into the valve body but not depress the valve itself. This is a common problem with the nozzle on its own. In the image, you can see that the nozzle (which we cut the tip off to show you) fits inside the valve body, but the valve pin fits inside the nozzle and so is not being depressed. This will result in a failed fill.
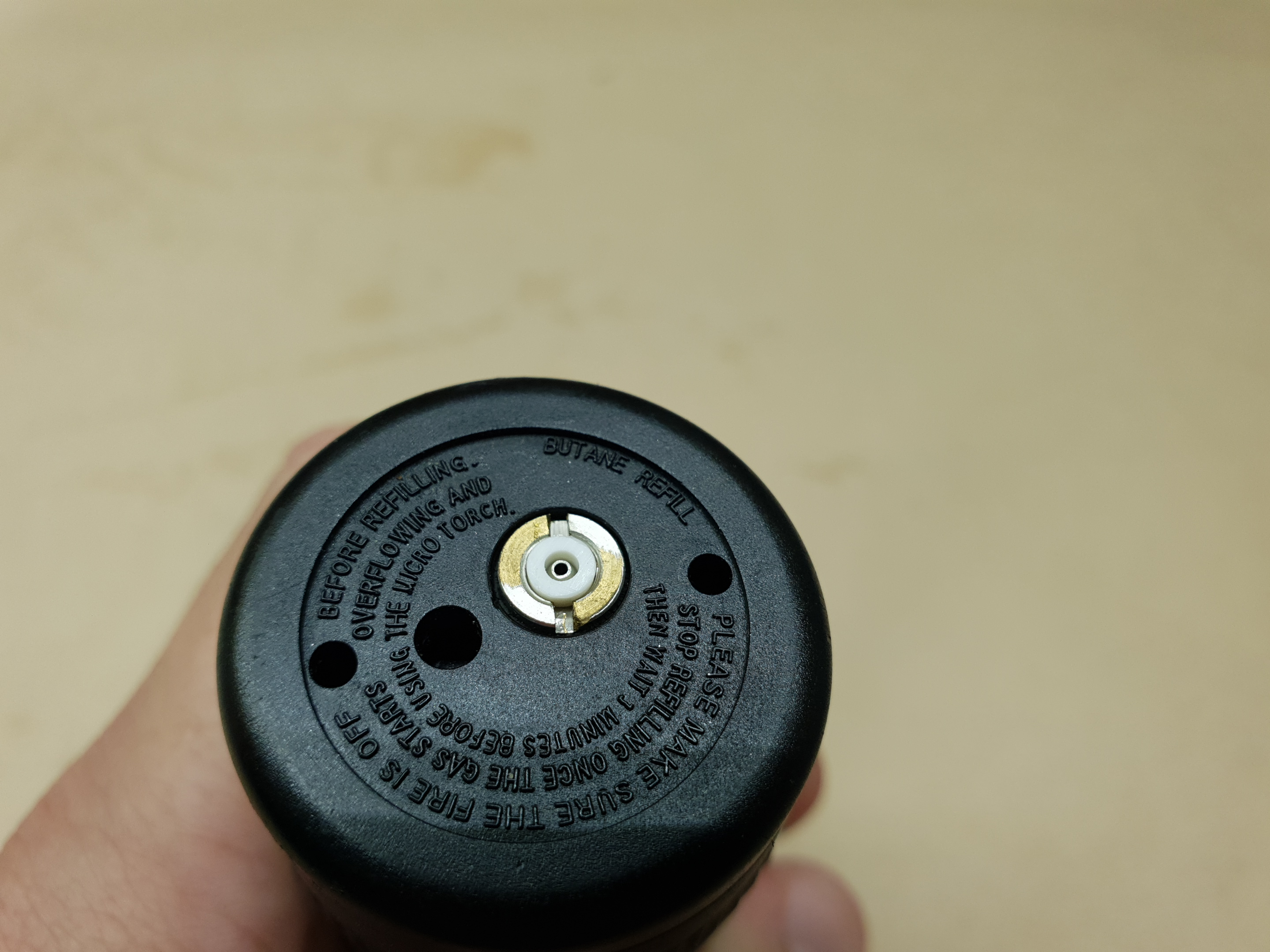
To fill the tool or lighter, hold the can with the correct adaptor onto the fill valve, with the tool upside down and the can upside down on top. Press down until you hear a faint hissing. This is the liquid gas moving through the valve. It may also sound like running water rather than hissing gas. When the tool is full, some gas will start to jet out the sides. Do not stop yet. A moment or two later, jets of liquified gas will start to vent from the valve and adaptor. Now, the tool is full and you can remove the refill can.
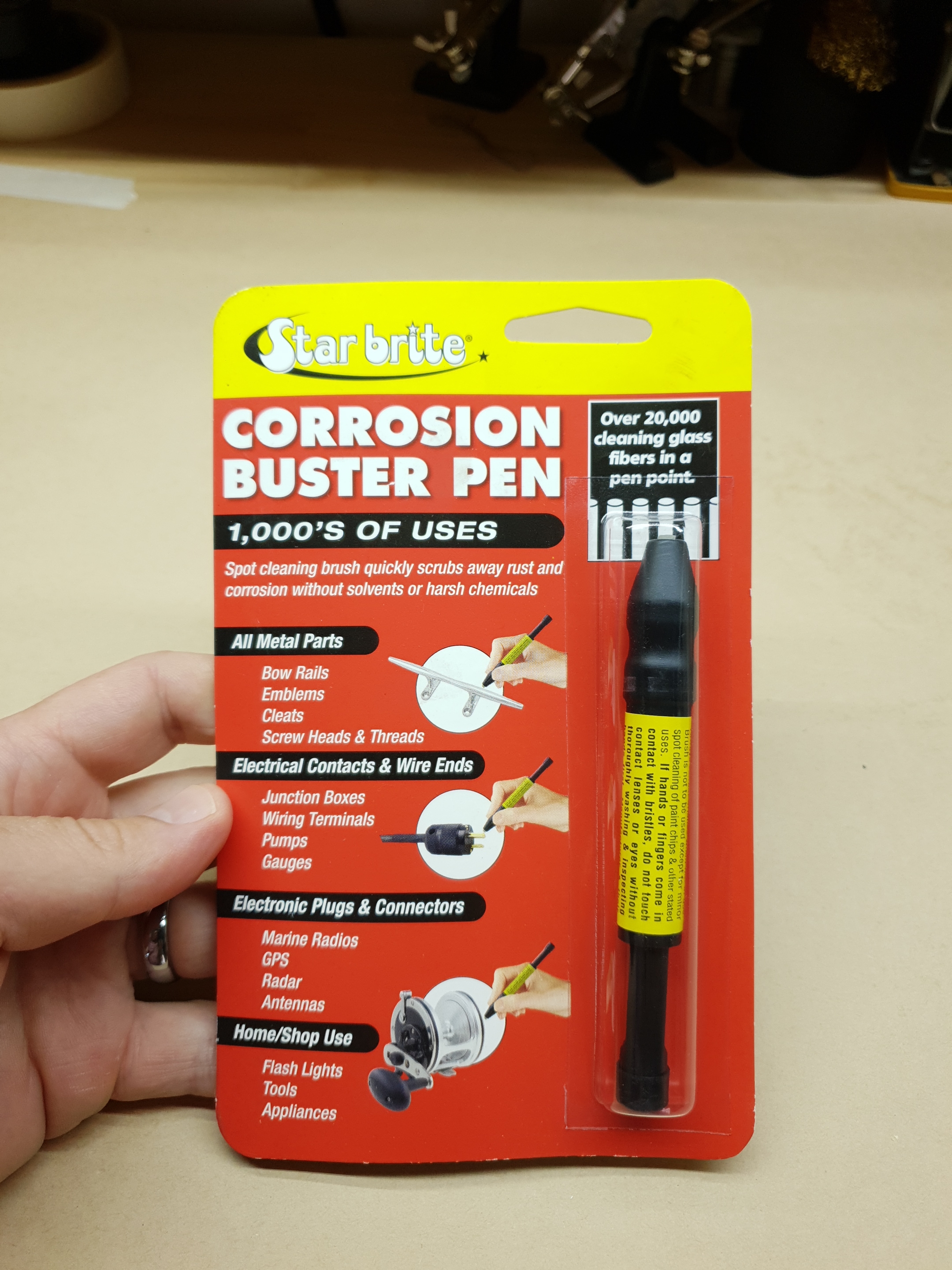
The NA1410 Corrosion Buster pen is a great tool that was just waiting for someone to invent it! Now that they have, the job of cleaning corrosion from small metal surfaces is much, much easier. Designed for small or fragile jobs where a brutal sandpaper, wire brush or even worse, a grinder are just unsuitable or too big, the corrosion buster pen is a retractable pen made up of 20,000 fine glass fibres. It mechanically scratches off corrosion but it does it much more finely and gently than even the finest sandpaper. In addition, it can be used on odd-shaped items like battery contact springs. No more ruined toys because the batteries leaked! Got an old camera you want to use but the battery compartment is full of green powder from where leaked batteries trashed it? Or are the contacts of a plug corroded on the surface and causing a poor contact? The corrosion buster pen is the answer.
To use it, twist the top so that just a small amount of the fibre bundle is protruding from the tip. They break off as a matter of normal use so if you extend it more than necessary, they will flex too much and snap even more or the whole lot. Rub gently at first, then with more pressure as needed, and move the pen around at different angles. Small airborne glass fibre particles are part of the process, so wear a dust mask, be careful of eyes (it's floating particles, not flying bits, so safety glasses will not help much), and clean up carefully afterwards! Also, consider gloves because the fine glass powder can be a skin irritant.
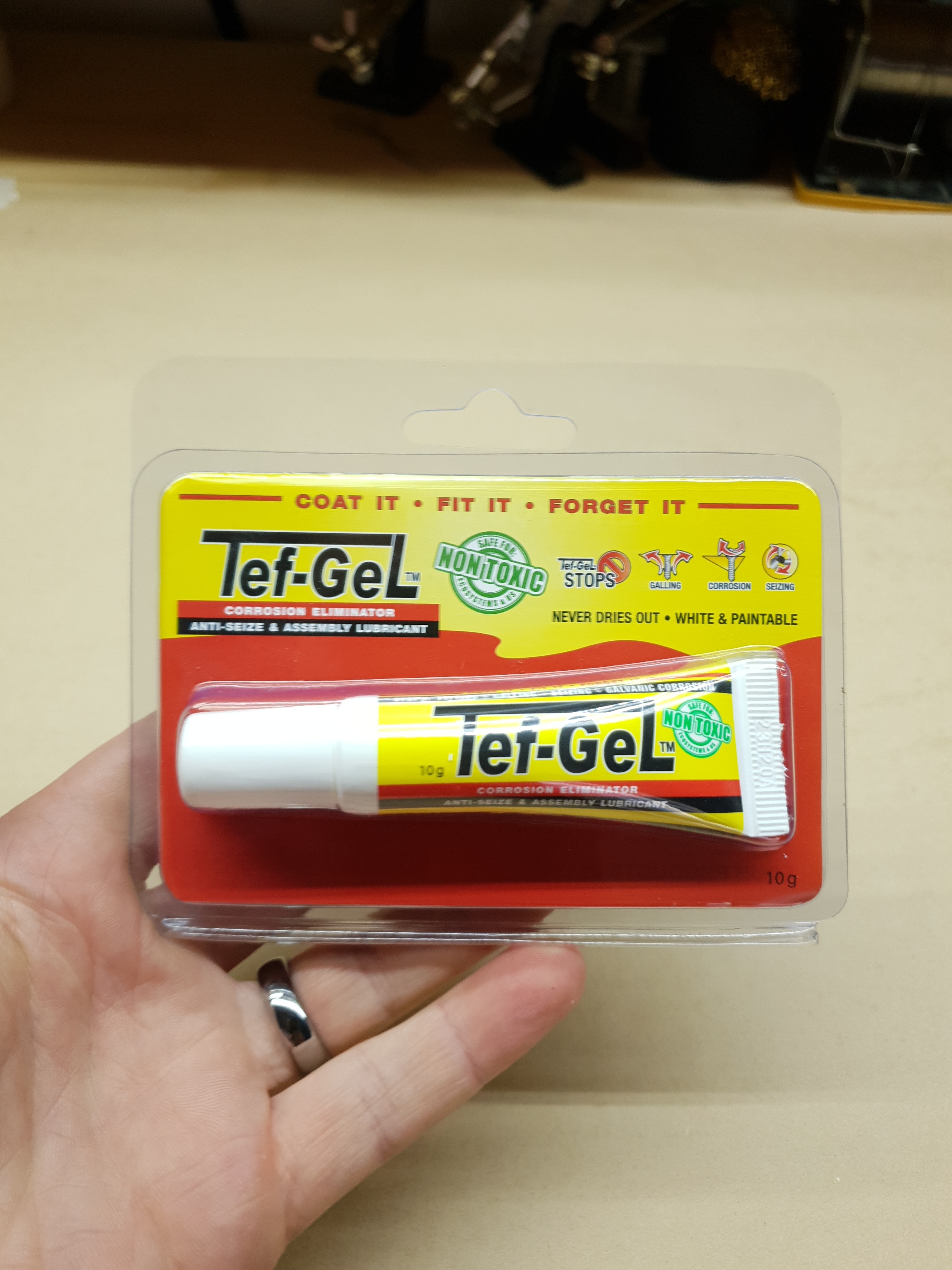
This product is designed for preventing the corrosion that naturally happens between different sorts of metals. All metals are electrically active. Down on the atomic level, different metals have different numbers of free electrons in their outer shells, with different energy bands. Even different grades of stainless steel are electrically different, thanks to the alloying materials.
The result is that when dissimilar metals are in contact, one metal wins most of the electrons. That leaves the other more susceptible to corrosion than before, and oxygen is totally happy to gain or give electrons to reach stability. Therefore, one metal oxidises more than it would on its own.
Tef Gel is a Teflon-like gel that can be applied to the surfaces between these metals. It is even suitable to apply to screws going into metal, as they are often a different metal to the one they are fixing into, and forms a film between the screw and the metal it is in. This electrically insulating thin film prevents the metals from electrically interacting with one another, and therefore helps prevent corrosion. In addition, the gel is resistant to heat, water, and salt, so it is great for outdoor fixtures and fittings.
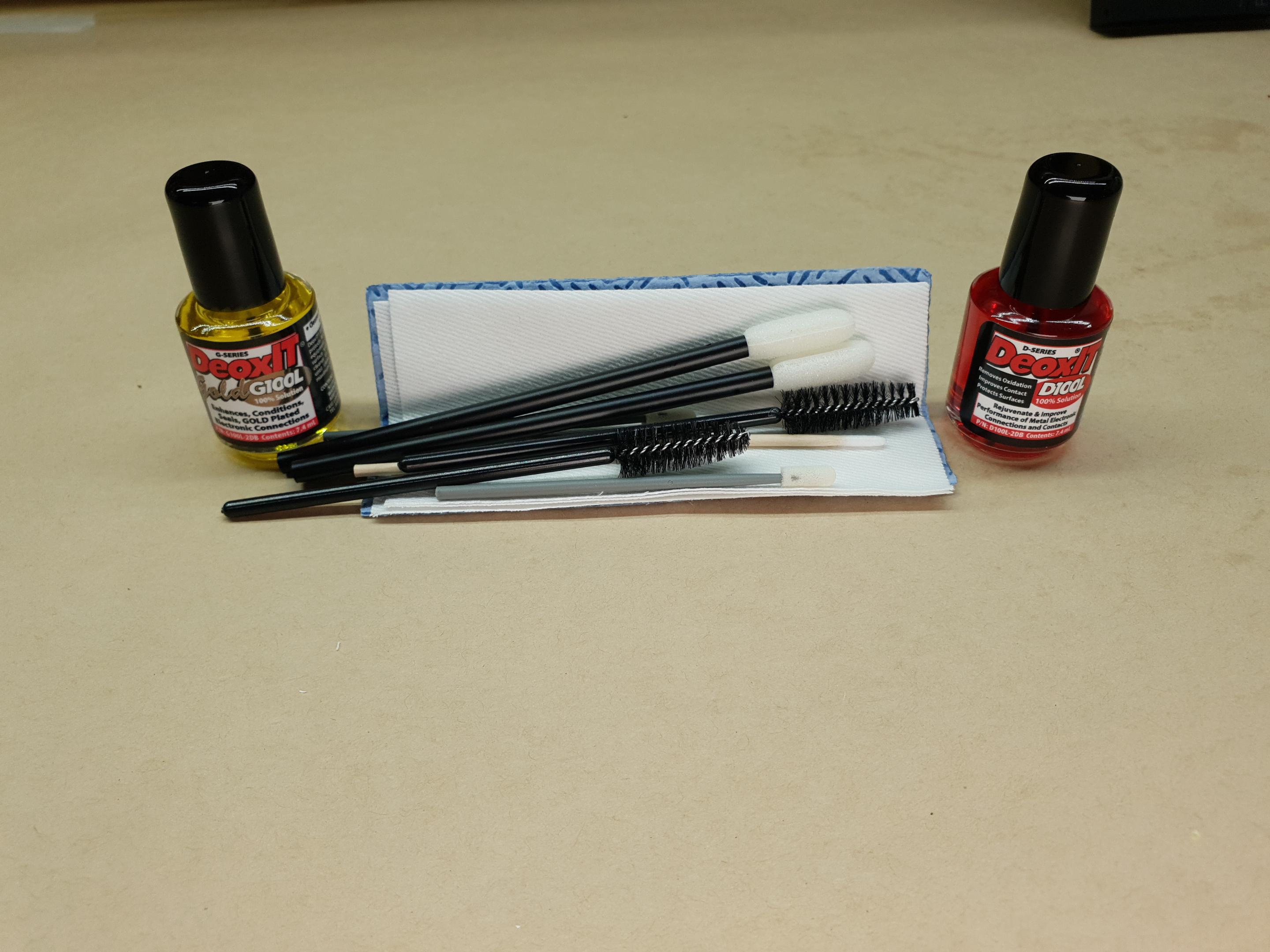
Sometimes, mechanically scrubbing oxidation from contacts is just not an option. Some are too small and fragile, while other times access is the issue, with not all of the surface reachable by a tool. The answer may be DeoxIT Connector or Contact Cleaner. This two-step kit comes with the two chemicals needed, along with a set of brushes and applicators to suit different plugs, sockets, and contacts, and a small lint-free cloth and work surface.
Corrosion on metals happens when oxygen electrically interacts with the metal, facilitated often by moisture. Oxygen has too few electrons in its outer atomic shell to be happy, and steals them where it can. Metals are less able to hang onto theirs, so oxygen can steal them. However, the oxygen bonds to the metal in this process. This causes the metal to physically change. Iron, for example, forms rust. The corrosion product is physically bigger, rarely holds the lattice structure of the metal and so flakes or powders off, and is not electrically conductive or as much so as the original metal. This is all bad news for contacts.
The red fluid goes on first and is a chemical corrosion solvent. It works to chemically separate the oxygen atoms and make them bond with each other rather than the metal. While this lifts corrosion from the surface, the damaged metal is not returned to the lattice so the surface may stay pitted. The red fluid is left on for a suitable time from a few minutes to overnight. This will be determined by each case, and no guide can be given. After the red fluid has worked, it should be a green or black colour. This is the dissolved corrosion. However, you may need to repeat the process for all the corrosion to be gone.
When it has, thoroughly wipe and dry the contact, before applying the yellow liquid. This is a protective film and you may need to wipe some excess off carefully, but otherwise, this stays on. That's it, you have restored a contact surface!
Similar projects you may be interested in