Telescope Dew Heater
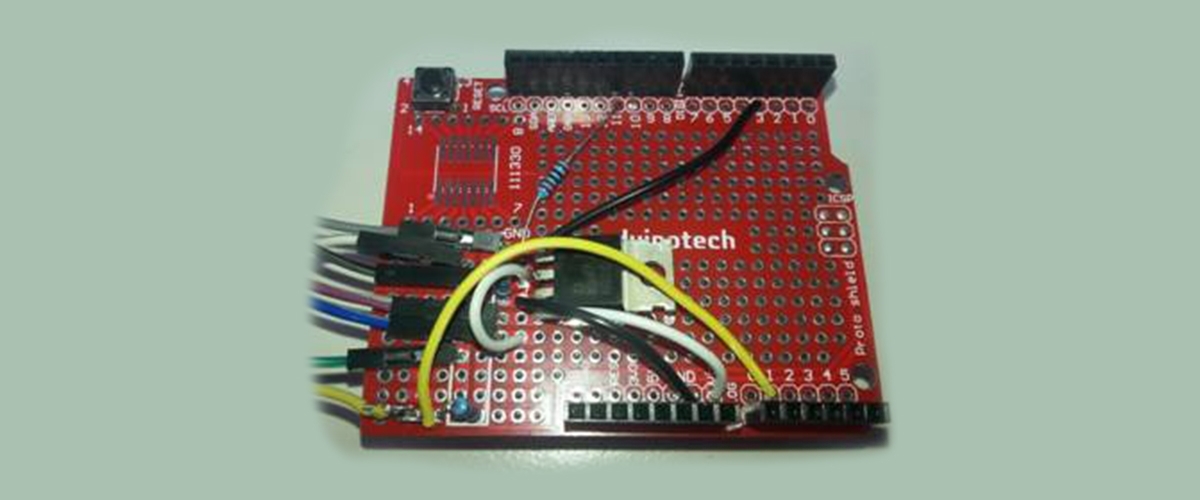
Summary
This project brings together a few Duinotech Modules and some other parts to create a versatile tool. Inspired by the Dew Heaters used on telescopes, it senses ambient temperature and humidity to control a small heater. Not just for telescopes, but anything that needs to avoid condensation.
Features Included:
- Programmable temperature setpoint
Temperature target can be set above ambient or dewpoint
Settings can be saved to EEPROM
Adjustable failsafe heater output to use if sensors are faulty
Comprehensive LCD info screen
By making use of as much data as possible, the unit uses no more power than necessary, and can even be run straight from a USB battery pack. It can run a set number of degrees above either dewpoint or ambient temperature. The backlight intensity is also adjustable in code and we've even designed a 3d-printed enclosure that will practically turn it into a professional looking unit.
Materials Required
1 | Arduino Compatible Temperature and Humidity Sensor Module | XC4520 |
1 | Duinotech Arduino Compatible 2 X 16 LCD Screen Display with Controller | XC4454 |
1 | Duinotech UNO r3 Main Board | XC4410 |
1 | 10kΩ Epoxy Dip NTC Thermistor | RN3440 |
1 | 10k Ohm 0.5 Watt Metal Film Resistors - Pack of 8 | RR0596 |
1 | 1k Ohm 0.5 Watt Metal Film Resistors - Pack of 8 | RR0572 |
1 | MOSFET IRF1405 N-Channel 55V 169A TO-220 | ZT2468 |
1 | Duinotech Arduino Compatible Prototyping Shield | XC4482 |
1 | 150mm Plug to Socket Jumper Leads - 40 Pieces | WC6028 |
1 | 39 Ohm 5 Watt Wire Wound Resistor | RR3264 |
Table of Contents
Future Improvements
There are a number of places where the heater could be improved, such as changing the default backlight setting to suit your application, or even making it one of the EEPROM settings. If you need more power, the recommended MOSFETs are capable of at least 5A at 24V. In that case, it would be recommended to run the power supply straight to the MOSFET circuit, and then feed VIN back to the UNO board. That way, the small PCB traces don't have to handle such a high current. An old laptop supply or 12V SLA could be options for this. As mentioned near the start, RCA sockets could be used to standardize the connections to those commonly used on heater bands.
Similar projects you may be interested in